A Comprehensive Approach to Attending To Stretch Wrap Maker Repair Service Obstacles
You understand that stretch wrap equipments are crucial for maintaining efficiency in product packaging procedures. Concerns can develop that interrupt performance. What are the finest strategies to guarantee your machines run smoothly?
Recognizing Common Stretch Wrap Maker Issues
When you count on stretch wrap machines for efficient product packaging, it's vital to recognize common problems that can interfere with operations - stretch wrap machine repair. One prevalent trouble is inconsistent tension, which can bring about poor wrapping and endangered lots security. If you notice the movie isn't sticking effectively, look for worn-out rollers or incorrect settings
Another problem you may encounter is film breakage, typically brought on by incorrect film kind or maker breakdowns. Regularly inspect the device for indicators of damage to avoid this.
In addition, watch on movie buildup or jams, which can stop manufacturing. Often, this happens because of imbalance or debris in the maker.
Last but not least, incorrect sealing can result in tons coming apart throughout transportation. Ensure your equipment is calibrated properly to preserve the honesty of your packages. By remaining attentive and addressing these concerns quickly, you can help with smoother operations.
The Importance of Routine Preventative Maintenance
Regular preventative maintenance is essential for keeping your stretch cover maker running efficiently and effectively. By routinely inspecting and servicing your equipment, you can find possible issues before they escalate right into pricey fixings. This proactive strategy not only extends the life expectancy of your device but also assures that it operates at peak performance.
You should schedule regular examinations to clean, oil, and change used elements. Maintaining your machine calibrated assists maintain suitable covering top quality, minimizes waste, and enhances performance. Additionally, documenting upkeep tasks produces a trustworthy background that can inform future decisions.
Do not forget the importance of training your personnel on maintenance ideal practices. When everyone recognizes exactly how to take care of the equipment, you minimize the risk of operator error leading to malfunctions. In other words, committing to normal preventative maintenance is a wise financial investment that pays off in decreased downtime and boosted efficiency in your operations.
Fixing Strategies for Quick Repair Works
Reliable troubleshooting strategies can substantially lower downtime when your stretch wrap maker experiences problems. Beginning by recognizing the signs and symptoms. Is the device not wrapping appropriately or is it making unusual sounds? As soon as you've identified the issue, refer to the driver's manual for assistance on typical problems and options.
Next, check the machine's setups and controls; sometimes, a simple adjustment can settle the issue. Evaluate the film tension and placement, as inappropriate configuration can bring about wrapping failings. Do not overlook electric connections; loose or broken wires can interfere with functionality.
If you're still encountering difficulties, consider running analysis tests if your maker has that ability. Record each step you take, as this can assist in future troubleshooting and fixings. Ultimately, don't wait to consult with a technician if you can not resolve the problem quickly. Efficient troubleshooting maintains your operations running efficiently and reduces expensive delays.
Training Operators for Effective Equipment Use
To ensure your stretch wrap equipment operates at peak efficiency, correct training for drivers is vital. When drivers understand the machine's functionalities, they can optimize its prospective and minimize downtime.
Urge them to practice under guidance, attending to any kind of inquiries or concerns they might have. Routinely scheduled refresher courses can keep their skills sharp and assist them adapt to any updates or adjustments in innovation.
In addition, impart a society of responsibility by encouraging drivers to report problems or recommend enhancements. This aggressive approach not just improves their self-confidence yet also adds to the total effectiveness of your procedures. With well-trained operators, you'll see fewer mistakes and raised productivity, guaranteeing your stretch cover maker stays a beneficial asset.
Constructing a Solid Communication Network In Between Teams
Well-trained operators can just perform at their best when there's a solid communication channel between groups. Reliable interaction removes misunderstandings and assurances everybody's on the same web page pertaining to equipment operations and repair needs. Motivate normal check-ins and meetings to talk about problems, share understandings, and address problems.
Utilizing technology, like messaging applications or collaborative platforms, can enhance real-time communication, making it less complicated to report troubles and share updates quickly. Designating clear duties and obligations fosters liability, enabling employee to get to out to visit here the best person when issues emerge.
Additionally, developing an open atmosphere where every person feels comfy sharing feedback can lead to cutting-edge services. By focusing on communication, you're not simply improving device efficiency; you're additionally building a cohesive team that interacts effortlessly. This collaborative spirit inevitably results in quicker fixings and lowered downtime, benefiting the whole operation.
Buying High Quality Replacement Components
When it pertains to keeping your stretch wrap machines, buying high quality substitute parts is essential for ensuring trustworthy performance and reducing downtime. Inexpensive alternatives may seem alluring, yet they often cause even more significant concerns down the line, costing you extra in fixings and lost productivity. By choosing high-quality components, you're not just taking care of a trouble; you're enhancing the general efficiency of your devices.
Additionally, top quality components are normally manufactured to stricter standards, which implies they'll fit far better and work even more accurately. This reduces the likelihood of unanticipated break downs, permitting your operations to run efficiently. Reliable vendors usually provide warranties, giving you peace of mind in your investment.

Evaluating Performance Information for Constant Improvement
To improve your stretch cover maker's performance, you require reliable data collection methods. By assessing performance metrics, you can determine locations for renovation and boost effectiveness. Identifying these opportunities not only enhances procedures however also reduces downtime and fixing costs.
Information Collection Strategies
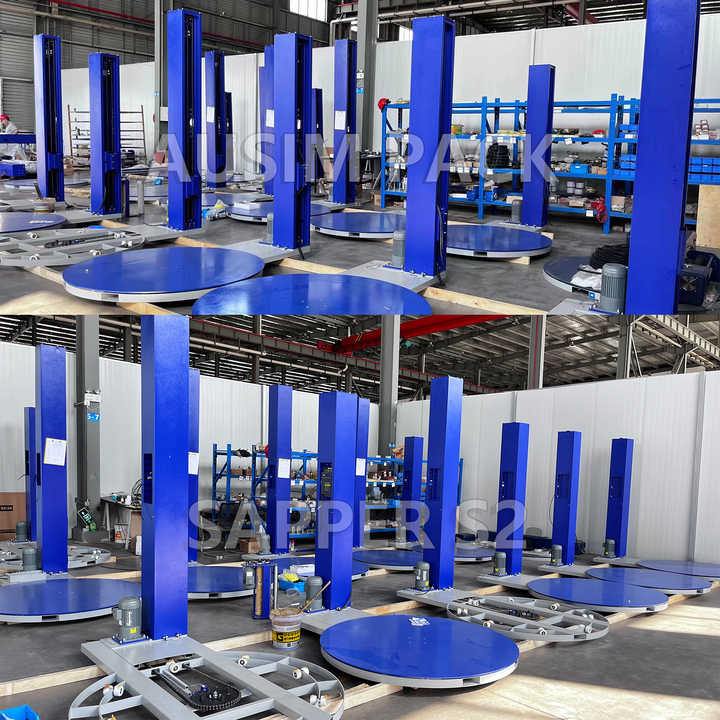
Efficiency Metrics Analysis
While assessing performance metrics, it's vital to concentrate on details information factors that directly influence your stretch wrap maker's efficiency. content Beginning by tracking cycle times, as they expose just how swiftly your device runs under normal problems. Monitor downtime occurrences to recognize patterns or recurring concerns that might need dealing with. Maintain an eye on film use, guaranteeing you're not squandering product, which can affect costs and performance. Additionally, evaluate output high quality by inspecting for disparities in the covering procedure. By examining these metrics consistently, you can identify locations needing interest and take proactive actions. This constant evaluation assists boost productivity, decrease costs, and eventually enhance your device's long life, bring about a more efficient wrapping procedure in general.
Recognizing Improvement Opportunities
As you assess efficiency data, you can discover important enhancement possibilities that enhance your stretch cover from this source maker's performance. Look for trends in downtime, cycle times, and wrap high quality. By recognizing patterns, you'll see which locations need interest. If frequent malfunctions correlate with certain operating problems, you can adjust procedures to mitigate these issues. In addition, contrast your information against industry criteria to determine your performance. Engage your team in discussions about the searchings for; their insights can expose useful solutions. Executing minor modifications based on this analysis can bring about significant gains in productivity. On a regular basis taking another look at and upgrading your performance data will ensure constant enhancement, keeping your procedures running smoothly and successfully.
Regularly Asked Questions
How Can I Inform if My Machine Requirements a Repair or Simply Maintenance?
To inform if your device requires repair service or simply upkeep, pay attention for uncommon noises, look for inconsistent efficiency, and examine for noticeable wear. If issues linger after upkeep, it's most likely time for a repair service.
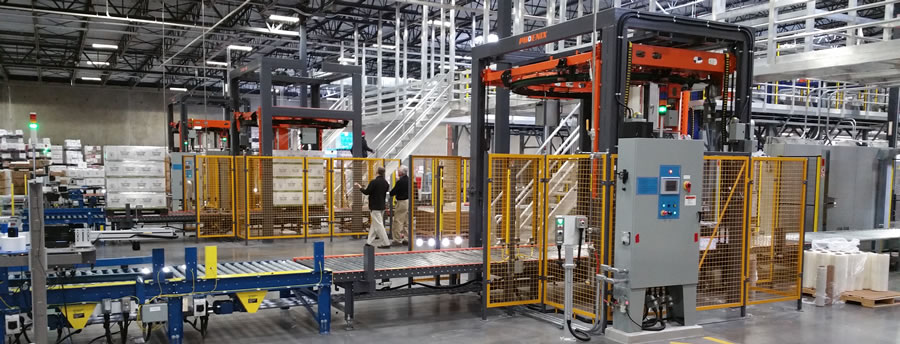
What Is the Average Life-span of a Stretch Cover Maker?
The standard lifespan of a stretch wrap equipment is commonly 5 to 10 years, relying on usage and maintenance. Regular treatment can expand its life, so watch on efficiency and address issues promptly.
Are There Certain Brands Recognized for Better Integrity?
Yes, some brands are known for their integrity. You'll discover that business like Signode and Lantech typically obtain positive evaluations - stretch wrap machine repair. Investigating customer responses can aid you select a reliable stretch wrap machine for your demands
What Are the Signs of Poor Operator Training?
If you see frequent errors, inconsistent covering, or safety and security cases, those are indications of inadequate operator training. Lack of comprehending regarding machine functions or failure to adhere to protocols can considerably affect efficiency and safety.
Exactly How Can I Discover a Certified Technician for Services?
To locate a certified service technician for fixings, ask for recommendations from industry peers, inspect on-line testimonials, and verify accreditations. You might likewise take into consideration contacting local devices vendors who frequently have trusted specialists available.
Conclusion
To sum up, tackling stretch cover equipment fixing obstacles requires an aggressive method. By prioritizing precautionary maintenance, offering extensive operator training, and spending in quality parts, you can substantially decrease downtime and enhance efficiency. Do not neglect the significance of strong communication between teams and continuous assessment of equipment result. By executing these approaches, you'll not just enhance wrapping quality yet additionally cultivate a culture of effectiveness and renovation in your procedures. Stay in advance of problems prior to they develop!